Cast your mind — and perhaps your Google Maps — to Mahé in Seychelles, 1500 kilometres east of the Kenyan-Tanzanian border in the Indian Ocean, where national carrier Air Seychelles is about to send its first Airbus A320neo away for maintenance after eighteen months of service.
On a chilly European morning we’re talking to Gustave Pragassen, the airline’s head of technical, from sunny tropical Mahé, about how Air Seychelles keeps its fleet — currently two Viking Air (formerly de Havilland Canada) DHC-6 Twin Otter turboprops for interisland hops and two Airbus A320neo jets for international routes — in tip-top shape to maintain vital air routes to and between the islands.
Some maintenance, and indeed all MRO for one of the airline’s two aircraft types, is done in-house. Air Seychelles is the only international MRO in the small island country, and it does full maintenance for the Twin Otters internally, from A to D checks. For the A320neo aircraft, it handles the A checks in Seychelles, with international contract MRO operators taking care of the more complex and involved work at scale overseas.
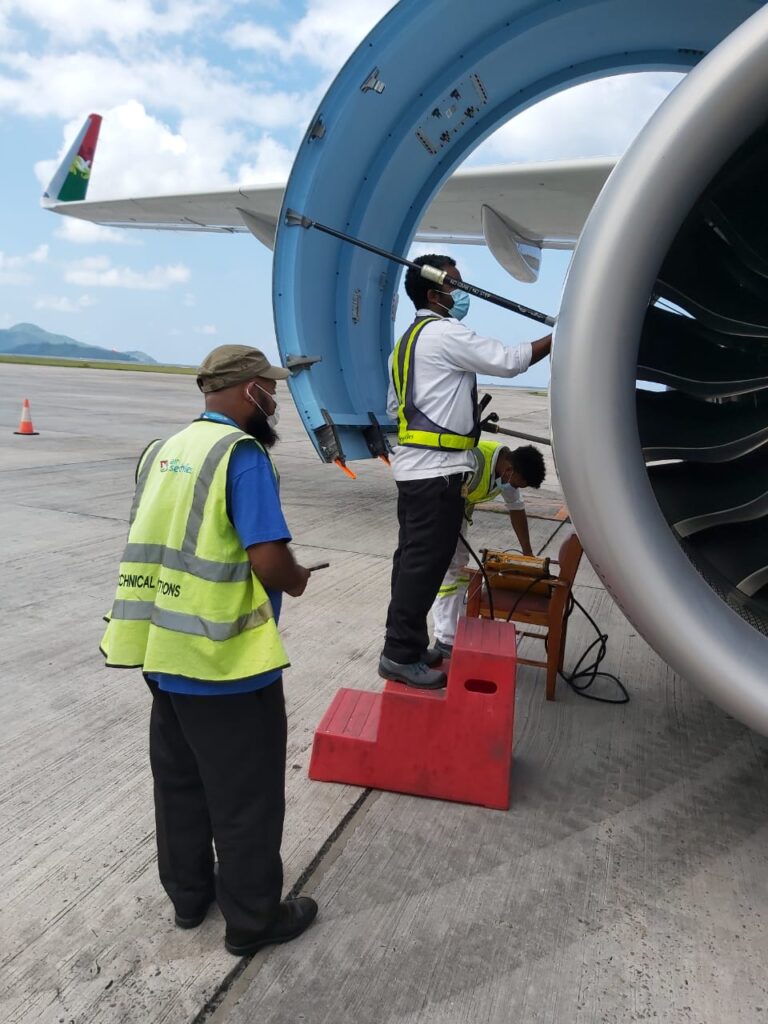
Image courtesy of Air Seychelles
When looking for an MRO, “we send out a request for proposal to several MROs around the world,” Pragassen explains. “We discuss their proposal and then at the end of the day we choose one that most suits our requirements. All MROs have to be EASA approved. This is a requirement under [the Seychelles Civil Aviation Authority].”
Typically, the work will be done by an in-house MRO of a partner airline that also operates the A320 family aircraft: SriLankan Airlines Engineering, for example, or Air India, or Etihad Engineering.
In addition to cost, Air Seychelles looks at turnaround time and what the MRO can offer in-house versus having to bring in specialists, which would add time and cost to the programme. These specialist areas include composite work, non-destructive testing, and cabin work — as well as whether the MRO has conducted similar work previously.
When the aircraft flies off to its MRO destination, “we typically have two or three representatives on the ground that oversee the maintenance. They don’t participate directly, but indirectly,” Pragassen says, with a key aim of the travelling staff being “to make sure that the check is done within the allocated budget that we have specified.”
Across the MRO function, Pragassen currently manages a team of 59 people within Air Seychelles: “I have eight managers and 16 certifying engineers. I’ve got 15 support staff like planners, back office staff, and stores. Then I have 22 technicians: these are non-certifiers, but they are qualified technicians that also work on the aircraft. “
The planners, technical planners and maintenance managers “manage the check, they build up the check package, and once they build up the check package, they discuss the check directly with the MRO. Once this is in place, then some of the planners and some of the maintenance personnel will form part of the oversight team that will oversee the check.”
At home in Mahé, Pragassen explains, “we are an EASA approved organisation for line maintenance.” That’s not just for Air Seychelles aircraft: the EASA approval opens doors for the airline to repair other operators’ aircraft, and Pragassen explains that all inbound operators’ regulators permit work to be done in Seychelles.
That’s particularly attractive for unexpected maintenance and repair requirements by other operators, owing to the islands’ remoteness. After all, having an aircraft grounded at an airport in the middle of the Indian Ocean without an approved MRO provider would be something of a problem for any airline.
For Air Seychelles, it means that “every flight out of Seychelles has to be an ETOPS flight,” Pragassen says. “So to be able to achieve that, to be able not to be grounded, we have to make sure that we have stock of every ETOPS required part in consignment in Seychelles because if you do get an ETOPS problem, then you can’t fly anywhere really. So our main stock typically consists of all no-go items, and all ETOPS components. So we have quite a variety of stock for the fleet, just to be able to get us out of Seychelles, if we had a defect.”
While it has an extensive holding of parts, Air Seychelles has yet to invest in the newest generation of digital tools for MRO, which Pragassen says is a function of both cost and the relatively small size of the fleet.
With the Twin Otters able to be maintained using relatively few digital tools, just two A320neos in the fleet, and a strong partnership regionally with Etihad Engineering — and of course daily flights from the UAE to Seychelles — any modern tool or piece of equipment can be leased from Etihad and arrive in Mahé within a day or two, with an accompanying operator if necessary.
“If it’s a very complex tool,” Pragassen explains, “then they will send an operator, who will typically arrive in the morning and leave in the evening.”
While that doesn’t leave time for a tropical overnight, Pragassen says that a couple of hours to relax on the beach while waiting for their return flight can be something of a draw for equipment operators.
More widely, staffing is one of the challenges that Pragassen works through on a regular basis: “when people go on leave, people go on sick leave, you find yourself suddenly short of manpower. In Europe, for example, you can easily get some contractors to come in within a day or two. But in Seychelles that’s not easy.”
Part of that is “the complexity of getting external workers to come here: you have to apply to the government, and by the time you get all the application through, get the permission, it takes a long time. Unless it’s well-planned ahead, then you’re okay,” Pragassen says. “But if you are in a very short — like a week or two weeks — lead time it will not happen. Normally, you have to apply at least two months in advance.”
Sometimes in aviation, and especially in the MRO world, complexity isn’t found in the advanced technological and digital tools at the bleeding edge of innovation: it’s around getting the right people in the right place at the right time.
Author: John Walton
Published: 1st June 2021
Join the Challenge
Getting the right people in the right place at the right time for the MRO world can prove difficult at times. Do you have similar challenges in your organisation? Join the discussion over in our Challenges Area.