Read our series of interviews with the people who are making the Yocova platform come alive. Here we speak to Chris Brady, CEO and Founder of Unum Aircraft Seating, and get the lowdown on aircraft interior design and manufacturing, the use of composites in aircraft, and some of the safety regulations that govern it.
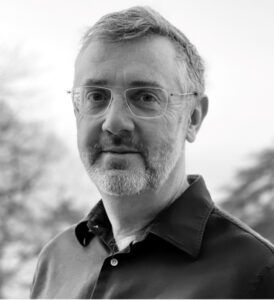
Chris Brady, CEO and Founder of Unum Aircraft Seating
Chris Brady is the CEO and Founder of Unum Aircraft Seating, an aircraft seat manufacturer on a mission to deliver maximum comfort with minimum weight, focusing specifically on providing high-quality business class seats.
Chris sits down with aviation journalist John Walton, to explain the intricacies of aircraft seat design and production, the history of regulations and safety standards for aircraft interiors, and the challenges faced in meeting them.
What is Unum, and what do you do in the aircraft seating market?
“We’re a manufacturer of business class seats for aircraft, based in Surrey in the UK. Unum is actually my second time around as I was previously CEO and founder of Acro Aircraft Seating, which makes economy seats for the other end of the plane. Now, we’ve gone up front and are trying to do something special up there too!”
What does the process of certifying a modern aircraft look like?
“If we compare modern regulations and standards to historic ones, today, it’s really focused on occupant injury. Historically, it was largely about how strong materials were and this was known in the industry as 9g certification, which meant that a seat was required to withstand force of up to 9g. About 25 years ago, a change in regulations was provoked by a fatal and tragic crash in the UK, when very strong seats ripped away from the tracks, injuring passengers and preventing them from escaping before the aircraft caught fire. Since then, there has been more focus on ensuring passenger survival and the 90 second rule, which is enough time to evacuate passengers from an aircraft if it catches fire.”
How about today’s safety standards?
“Today’s seats are required to withstand a dynamic 16g force. The seats are tested by simulating a load that could be expected in an accident that could be survivable, and the twists and turns that would be brought about by the aircraft buckling. The introduction of the new certification fundamentally changed the way aircraft seats were designed to focus on passenger survivability, and then flammability is of course also key to ensure a fire is prevented for the 90 seconds to be able to get everyone down the slides and off the plane.”
Can you explain about HIC and Nij?
“These are part of the 16g test we carry out by placing a crash test dummy on the seat and applying the dynamic force. HIC stands for Head Injury Criteria and this is used to assess the likelihood of a head injury in the event of a crash and Nij is the neck injury criterion. A further assessment has also been introduced which includes some new twist and lower leg criteria too, which was adopted in the US in 2019 under the FAA and by the European Aviation Safety Agency in 2022, so it’s pretty hot off the press. In the UK, post-Brexit we have the Civil Aviation Agency and they are in the process of adopting similar, which is expected to come into UK law towards the end of the year.”
Can you explain the use of composite materials in aircraft interiors? How do composite materials change the certification process?
“Interesting question. When we look at metal, it’s easy to mass produce, with predictable characteristics. Composites are a completely different kettle of fish. Their performance is one thing, but manufacturing processes vary and so process control in manufacturing is really important. They have to pass flammability and heat release tests, but the quality of manufacturing is key. With a metal, you can see if it’s damaged as it would be dented or bent, but with composites you can’t because they are layers of different materials, so when it’s damaged it can become what’s called ‘’delaminated’ and therefore weakened in an area of impact. The regulators are therefore keen to understand what the consequences of damage might be, so you must undertake a failure mode effects analysis. If the damage is likely to be difficult to detect visually, you need to put in place a frequent inspection regime and this is known as continuous air worthiness. While it is possible to make a composite seatback, the maintenance that comes with it means that it’s just not worth it.
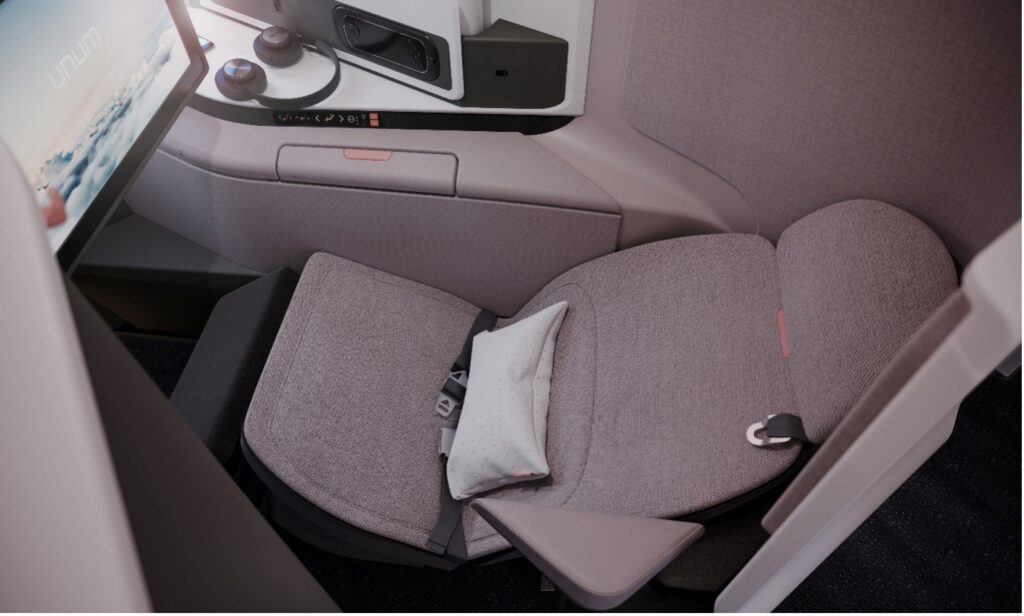
Unum Seating – typical seat design
Composites are really useful however, particularly in business class, where we are always chasing space to make room for additional paneling for things like beds and foot boxes. With composites, we can trace out funky shapes and curves to fit into the cabin. And it really comes down to the economic side of things. If we were to make these shapes in metal, the tools would be so costly that it wouldn’t be viable for relatively few seats. To fit out the cabin or a few cabins within a fleet would require different seat shapes and therefore multiple tools, which cost around £250,000 per shape. With composites, the tooling is far cheaper, at around a tenth of the price of metal.
Composites that we come across often, for example, in golf clubs or bicycles are usually made from a composite called epoxy, but the problem with this is that it burns fast. Phenolic based composites are better but are difficult to handle and work with. When phenolic based composites are heated, a pinhole effect forms, which is unappealing to the eye, so for aircraft paneling made from this, wallpaper is usually applied over it. It’s also tricky because if you have too many pinholes, you have to apply filler, but if you apply too much filler, you risk failing the certification test and so on.
So, you probably now get an idea of the challenges we face in the aircraft interiors world!”
For more information, to contact or to collaborate – then connect with Chris on Yocova via his personal profile.
Author: Yocova, with special thanks to John Walton
Published 19 September 2023
Watch John Walton and Chris Brady discuss these topics in person.
To view the full podcast episode register for Free Yocova Membership,
log in and head to Workspace > Learning.