Read our series of interviews with the people who are making the Yocova platform come alive. Here we speak to Nina Schulz, Managing Director of the Independent Aircraft Modifier Alliance, about the challenges the pandemic presented to MROs and the wider aviation industry, her observations on how the industry is recovering, and how she foresees technology will serve to support the industry in future.
Nina Schulz joined the Independent Aircraft Modifier Alliance (IAMA) in January 2022 after a long career spanning 19 years in a variety of roles at Germany’s flagship carrier Lufthansa. The IAMA was founded just before the pandemic caused major disruption in the aviation industry globally and was established by a small alliance of members in the aircraft modification and retrofit specialities. The IAMA went on to generate wider interest in the sector and attract new members and is now on a mission to strengthen and prove the value of the modification market.
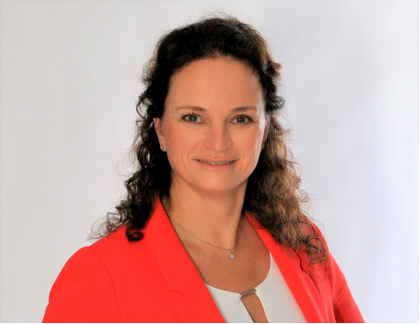
Nina Schulz, Managing Director of the Independent Aircraft Modifier Alliance
Now, a year into her role at the IAMA, Nina shares some interesting observations with our resident aviation journalist John Walton about her insights into the effects the pandemic had on aviation, what post-pandemic recovery is looking like, and how she thinks things can be better in future. Read on to find out more.
Can you tell us a bit more about IAMA and what you do?
“We’re basically on a mission to address aircraft modification challenges and this is structured around three key areas – educate, simplify and endorse. And we believe that our overall mission can be achieved through our initiatives that aim to create a distinct, transparent and independent market for aircraft retrofits.”
How do you see the current state of MRO within the aviation industry
“The aviation industry obviously took a huge hit during the COVID-19 pandemic, and of course the MRO and modification industries suffered greatly too. But aviation has made a significant comeback as people want to travel, see the world and visit friends, relatives and business partners. So interestingly, what we’re seeing is that MRO is actually in very high demand. So much so that it’s actually turning into a seller’s market, because the capacity there is not enough to meet demand. Aircraft that appeared doomed and were parked up during the crisis, even old aircraft, are now needing to be brought back into operation. And the other interesting thing about that is that relationships between business partners that survived during the crisis are doing well post-pandemic. But then aviation really is a people’s business.”
How has MRO capacity evolved?
“I think with the unprecedented situation the pandemic presented, we expected more MRO participants to go out of business. Of course, some have vanished and others emerged, but what’s interesting is that we haven’t seen the damage to quite the extent we expected; in fact, some of the big players have turned the crisis into an opportunity and have used it to grow and expand their business. The biggest problem right now is staff shortage. Labour shortages are affecting a whole range of industries at the moment, but I think in aviation it’s more critical than some, because you need experts and highly trained staff, and that quite simply takes time to achieve. Aviation lost a huge number of skilled people during the pandemic and that, quite simply, continues to have an impact on capacity.”
Are MRO providers looking to recruit from within the industry?
“Well, in these kinds of situations you need to look both left and right, but also at the kind of environment and opportunities you are offering. Of course, it’s good to attract back skilled people who have left the industry, and in terms of attracting new talent, that’s important too, but aviation is a very safety-focused industry, so to train up brand-new talent will take time. I think the sector could benefit from reviewing some of its processes and consider some kind of cross qualification to open up new opportunities, but again, this will take some time, since safety cannot be compromised. One thing I do feel strongly about, though, is making the workplace and conditions attractive and making work interesting to attract people into it. And I think that’s really important in terms of the younger generations.”
What are employers offering now to attract talent?
“I’m not sure that things have changed that dramatically over these past years. There’s still a ‘shopfloor’ and an ‘admin’ side of things and I think the opportunities these workers get need to be carefully balanced. A lot of the administrative side of things was able to be worked on from home, and may have expectations to continue doing so, but those working in, for example a cold hangar, have no option but to return to the workplace, so I think companies need to be mindful about the working culture they create and that it is balanced within the facilities. But I think that where there are labour shortages within our industry, it will push automation and technology forward and help us to develop new techniques.”
Can you tell us about those new technologies and which ones IAMA is currently discussing?
“On the ‘shopfloor’, there’s the opportunity to deploy technology such as drones to carry out critical safety inspections on the top of aircraft for example. This would help to ease and streamline processes and make work safer and more efficient. I think technology excites people too. One of the things I find fascinating is the use of exoskeletons, to make working life easier. And the more you do to take the burden off people, the nicer their working conditions become.
“In terms of administration and planning, documentation is a big deal, since so much of aircraft admin requires literal paperwork. I think the more we work to introduce processes and documentation being supported by automation and artificial intelligence (AI), the better things will become in future.
“And then with planning, I think machine learning is going to help us a great deal. As we have fewer people who are experienced and knowledgeable about aircraft, perhaps machines will be what we need, at least to ease the work and free up human capacity for more extensive troubleshooting.”
When you talk about admin, do you think there’s an opportunity for aviation to become paperless?
“There are technologies under development at the moment that greatly support this. And of course it is great that our industry is heading in a paperless direction. While I think automating and digitalising these processes will bring about efficiencies and improve worker satisfaction, unfortunately at the moment we are stuck with paper, while also trying to transition, so that creates an added burden on staff right now.”
How about data ownership? Are there issues between, for example owners and operators?
“That’s actually a really hot topic right now and people really need to be aware of this. First of all, asset owners need to make sure they get their rightful share of data and that they own it and not anyone trying to sell it to them. And this applies not just to aircraft, but also to engines and components. This data is needed to keep control over your asset. At IAMA, we’re firm believers in transparency and fairness, but also intellectual property (IP). And that’s not just limited to OEMs – other companies should also have their fair share in it.”
We’ve heard a lot about new aircraft in recent years. But how about MRO maintenance packaging?
“Maintenance packages tend to be a bit different between older and new-generation aircraft. But in general, we are looking at a more modularised approach, which we hope will bring about shorter downtimes and a faster path back into operation. A kind of lighter packaging, which of course won’t mean things will be done overnight. But striving to achieve this lighter, more efficient checking process will of course put more pressure on the MRO, since repair and maintenance requests need to be made through the OEM. All of this can slow things down, and that’s one of the reasons we’re striving to drive more transparency between players in the industry, to try to do all of this more efficiently.”
What are you expecting to see evolve within the industry over the next ten years?
“Well, there’s speculation and also some commentary around whether the number of flights should be reduced, and I know there is some talk about reducing domestic flights in Europe. But, as I mentioned earlier, demand continues to be high as we move beyond the pandemic.
“In terms of how I think things will look operationally, I think we’ll see a lot more automation in aircraft hangars, for example, but I still think we’ll need to have people there and ready to do the real work and troubleshooting on aircraft. And as I mentioned before, I do think there’s room for devices such as drones to help us do things better and more easily. I’m sure there will be a lot less paper eventually and a lot of people using tablets and mobile computers, but I don’t think we are really going to get near a fully automated industry just yet.”
For more information, to contact or collaborate…
You can contact Nina on Yocova via her personal profile.
Watch John Walton and Nina discuss these topics in person courtesy of our Yocova on Air episode.
To see the full video podcast simply register for Yocova Membership, log in and head to Workspace > Learning.
Author: Yocova, with special thanks to John Walton
Published 02 May 2023